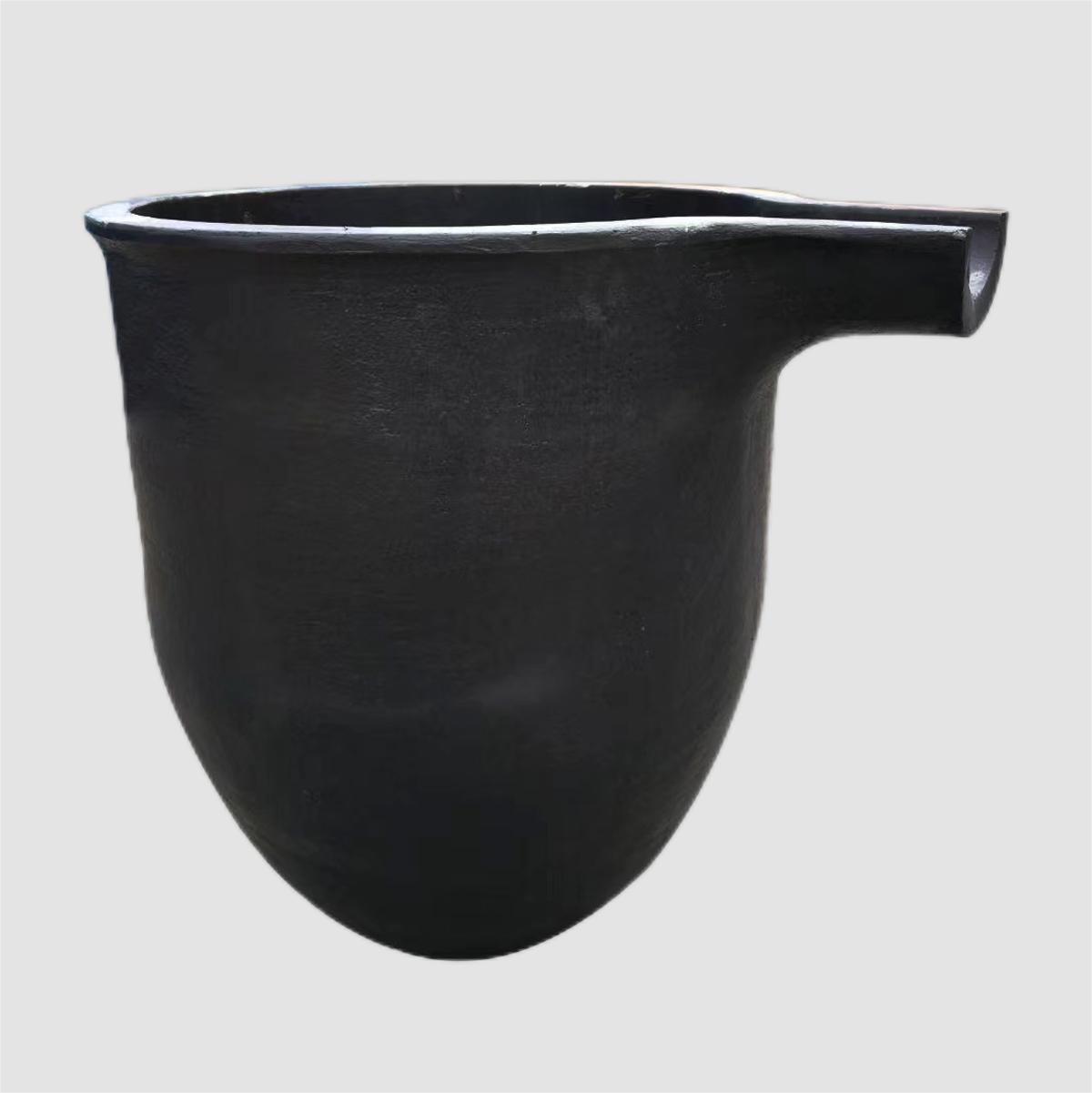
1.4二次研削
ペーストは押しつぶされ、粉砕され、数百から数百マイクロメートルのサイズの粒子にふるいにかけられ、均等に混合されます。プレスパウダーと呼ばれるプレス材料として使用されます。二次研削のための機器は通常、垂直ローラーミルまたはボールミルを使用します。
1.5形成
通常の押し出しや成形とは異なり、アイソスタティックプレスグラファイトコールドアイソスタティックプレステクノロジーを使用して形成されます(図2)。原料粉末をゴム型に入れ、高周波電磁振動を通して粉末をコンパクトします。密閉後、粉末粒子を真空にして、それらの間の空気を使い果たします。水や油などの液体媒体を含む高圧容器に入れ、100〜200MPaに加圧し、円筒形または長方形の製品に押し込みます。
Pascalの原則によれば、水などの液体媒体を介してゴム型に圧力がかかり、圧力はすべての方向に等しくなります。このようにして、粉末粒子は金型の充填方向に向けられていませんが、不規則な配置で圧縮されます。したがって、グラファイトは結晶学的特性において異方性ですが、全体的に、等張力のプレスグラファイトは等方性です。形成された製品には、円筒形と長方形の形状だけでなく、円筒形とるつぼの形もあります。
等造型プレス成形機は、主に粉末冶金産業で使用されています。航空宇宙、原子力産業、硬い合金、高電圧電磁などの高級産業の需要があるため、アイソスタティティックプレス技術の開発は非常に速く、3000mmの動作中のシリンダー内径、高さ5000mm、および600MPAの最大作業圧力を備えた冷たいシリンダープレスマシンを製造する能力があります。現在、等積プレスグラファイトを生産するために炭素産業で使用されている寒冷等等型プレス機の最大仕様はφ2150mm×4700mmで、最大作業圧力は180MPaです。
1.6ベーキング
焙煎プロセス中に、凝集体とバインダーの間に複雑な化学反応が発生し、バインダーが大量の揮発性物質を分解して放出し、凝縮反応を起こします。低温予熱段階では、生の生成物が加熱により拡大し、その後の加熱プロセスでは、凝縮反応により体積が縮小します。
生の製品の容積が大きいほど、揮発性物質を放出することはより困難になり、生の製品の表面と内部は温度の違い、不均一な熱膨張と収縮を起こしやすく、生の生成物の亀裂につながる可能性があります。
その微細な構造のため、等造型のプレスグラファイトは特に遅い焙煎プロセスを必要とし、特にアスファルト揮発性物質が急速に排出される温度段階では、炉内の温度は非常に均一でなければなりません。加熱プロセスは注意して実行する必要があります。加熱速度は1°/hを超えない、炉内の温度差は20°未満です。このプロセスには約1〜2か月かかります。
1.7含浸
焙煎中、コールタールピッチの揮発性物質が排出されます。微細な毛穴は、ガスの排出と体積収縮中に製品に残されており、そのほとんどすべてが開いた毛穴です。
体積密度、機械的強度、導電率、熱伝導率、および製品の耐薬品性を改善するために、圧力含浸方法を使用できます。
製品を最初に予熱し、その後含浸タンクで掃除機をかけ、脱気する必要があります。次に、溶けたコールタールアスファルトが含浸タンクに加えられ、加圧されて、含浸剤アスファルトが製品の内部に入ることができます。通常、アイソスタティックプレスグラファイトは、含浸焙煎の複数のサイクルを受けます。
1.8グラフィット化
焼成された製品を約3000個に加熱し、炭素原子の格子を整然と整理し、炭素からグラファイト化と呼ばれるグラファイトへの変換を完了します。
グラフィット化方法には、アチソン法、内部サーマルシリーズ接続法、高周波誘導法などが含まれます。通常のアチソンプロセスには、炉から積み込まれ排出されるには約1〜1.5か月かかります。各炉は、数トンから数十トンのロースト製品を扱うことができます。
投稿時間:2023年9月29日